Engineered Systems Applications
Reliability & Throughput
System Reliability and Process Throughput Analysis
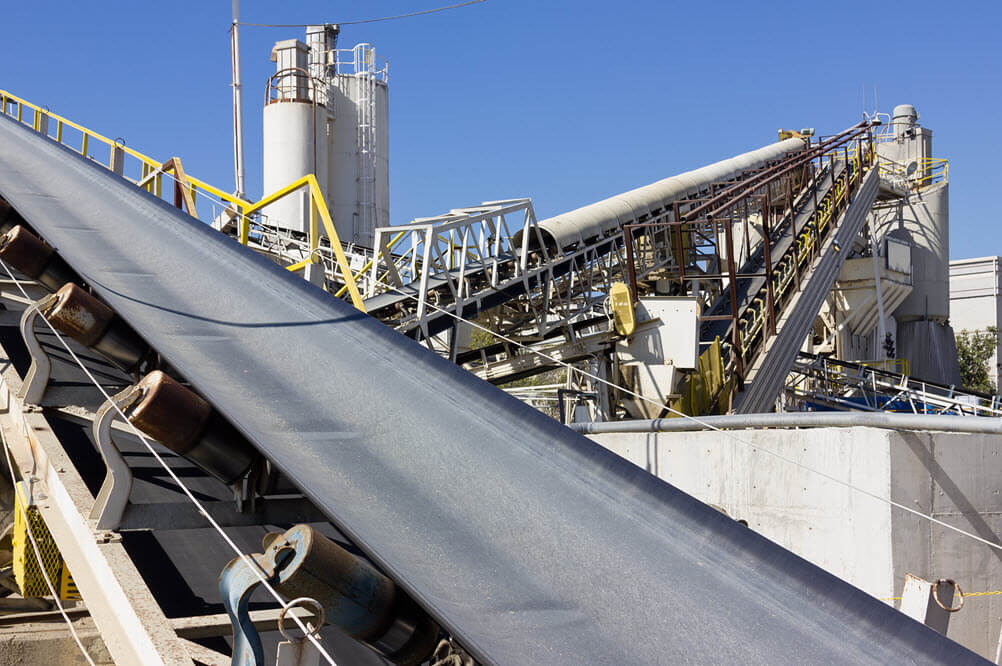
For many engineered systems, it is necessary to predict measures such as the system's reliability (the probability that a component or system will perform its required function over a specified time period) and availability (the probability that a component or system is performing its required function at any given time). For some engineered systems (e.g., processing plants, transportation systems), these measures directly impact the system's throughput: the rate at which material (e.g., rocks, chemicals, products) move through the system.
Reliability models are frequently used to compare design alternatives on the basis of metrics such as warranty and maintenance costs. Throughput models are typically used to compare design alternatives in order to optimize throughput and/or minimize processing costs.
By combining the flexibility of a general-purpose and highly-graphical probabilistic simulation framework that can directly model the movement of material through a system, with specialized features to support reliability analysis, GoldSim allows you to create quantitative and transparent reliability and throughput models to allow you to ask "what if" questions regarding various designs and make defensible risk management decisions.

These analyses are facilitated by the GoldSim Reliability Module. The fundamental outputs produced by the Reliability Module consist of predicted reliability metrics (e.g., reliability and availability) for the overall system, and for individual components within that system. The Reliability Module tracks and analyzes failure scenarios, which allows for key sources of unreliability and risk to be identified.